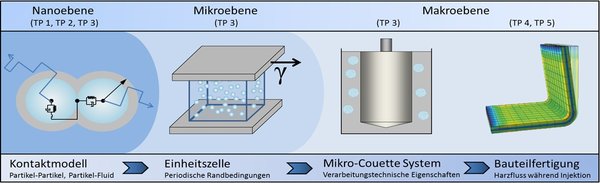
Subproject 3: Flow behavior of nanoparticulate epoxy resin suspensions
Subproject 4: Impregnation process of gradually nanoparticle-reinforced structures
Project leader: Prof. Dr.-Ing.
Funding period: 05/2014 - 04/2017
Funding body: DFG
Funding code: Zi 648/42-1
Contact: Dr. rer. nat. Tatjana Artys (SP 3), M.Sc. Dilmurat Abliz (SP 4)
Disperse properties, such as primary particle and aggregate size and particle size distribution, aggregate structure, primary particle morphology and surface functionalization of particles essentially determine the processing and application properties of continuous fibre reinforced nanocomposites (CFRC). However, models for describing this relationship across scales only exist in rudimentary form. The fundamental question to be answered is how the disperse properties affect structure formation along the process chain and the desired processing and application properties. Key parameters that determine the processing limits of nanoparticle epoxy resin suspensions to fiber-reinforced nanocomposites are the flow properties of the epoxy resin suspension and its reaction kinetics. For example, high suspension viscosities and short reaction times severely restrict the production of large or complex components. Decisive for the flow behavior and thus the processing limits are the processes and mechanisms on a micro scale, especially at solid/liquid interfaces. The interactions between particles and the surrounding fluid are of particular importance for the reaction time. These micro-scale interactions can be described by coupling CFD and DEM simulations and using suitable contact models for the interactions. To describe the rheological properties in nanoparticle epoxy resin suspensions, TP3 will set up and verify models that fulfill the important and demanding approach of cross-scale description. The models will be functions of aggregate structure, primary particle morphology, particle-particle interactions and reaction time. Subproject 3 is thus assigned to the second level of the research group, Influence of nanoparticles on polymer processing.
The main tasks of SP4 are the design of the preform and the development of new sprue strategies in order to produce a gradient material with a defined particle distribution and consequently
with specifically adjusted mechanical properties in liquid composite molding (LCM) processes such as resin transfer molding (RTM) and vacuum-assisted resin infusion (VARI). Permeability measurements are used to experimentally investigate how an NP-filled epoxy matrix influences the impregnation of the preform during resin infusion. The empirically determined data are then used to characterize and model the influence of nanoparticles on the flow properties during component production and are presented by means of microscale simulation of the flow of the NP-reinforced uncured epoxy matrix in a roving structure. The results obtained in SP4 are closely related to the findings from SP3 and will in turn provide the partners in SP5 and 6 with the basis for verifying factors influencing the nanoparticles on the fiber-reinforced plastic composite using suitable test methods and developing the necessary manufacturing concepts. In cooperation with SP1, the influence of the nanoparticles on the flow properties and particle movement during impregnation will be demonstrated using analytical methods.